The Best Strategy To Use For Alcast Company
The Best Strategy To Use For Alcast Company
Blog Article
Alcast Company Things To Know Before You Buy
Table of ContentsSee This Report on Alcast CompanyTop Guidelines Of Alcast CompanyRumored Buzz on Alcast Company10 Simple Techniques For Alcast CompanyThe 6-Minute Rule for Alcast CompanyFascination About Alcast CompanyThe Best Strategy To Use For Alcast Company
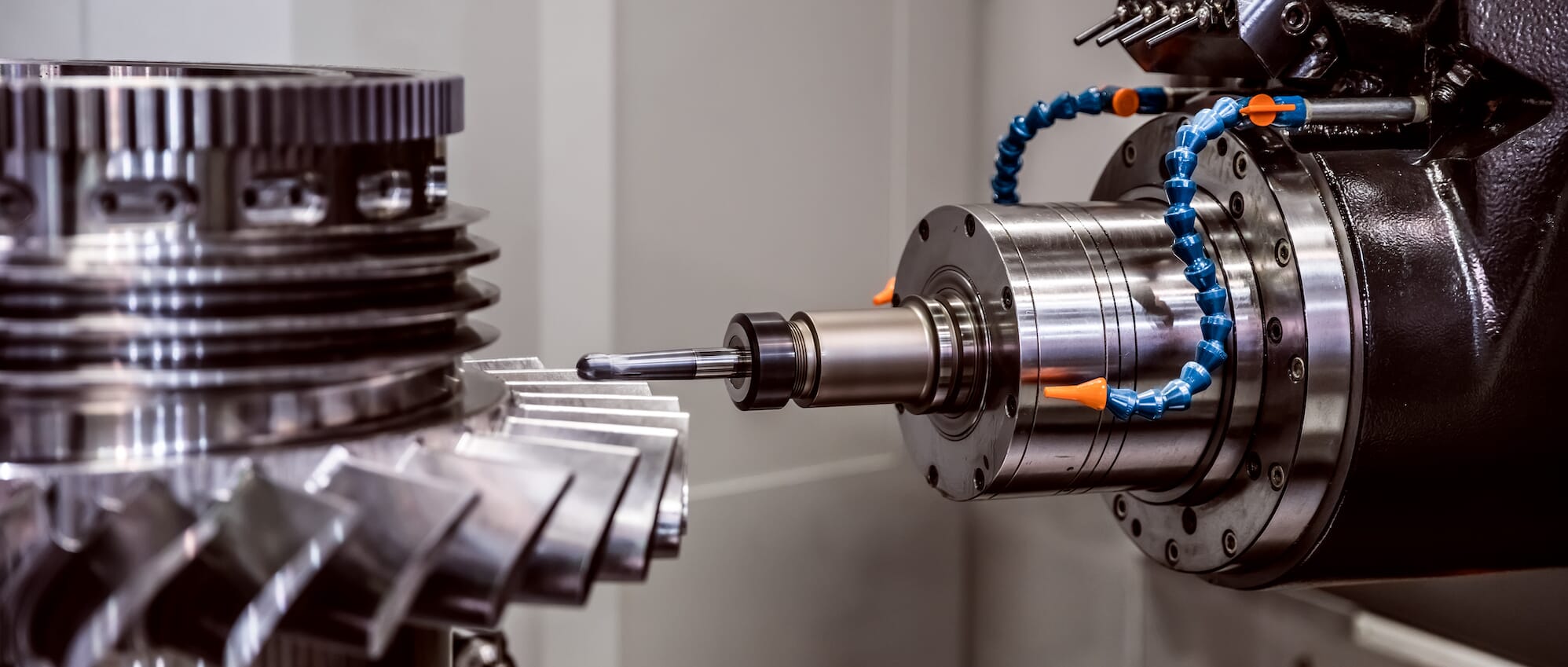
If you assume that a wrought alloy might be the most effective for your job, take an appearance at several of our posts that discuss more about details wrought alloys, such as Alloy 6061 and Alloy 6063. On the various other hand, if you assume a cast alloy would certainly be much better for you, you can discover a lot more regarding some cast alloys in our Alloy 380 and Alloy 383 posts (coming soon).
Our Alcast Company Ideas
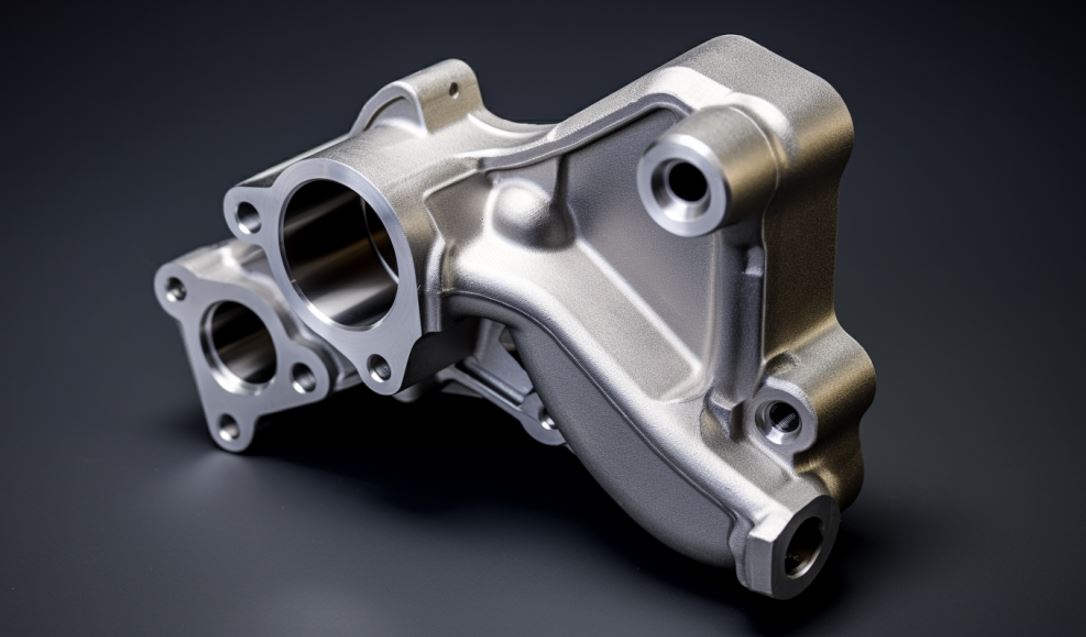
Having the experience and market knowledge to engineer your castings for optimum manufacturing and high quality end results will streamline the job. Making aluminum spreading requires a facility collection of procedures to accomplish the ideal results. When choosing a new light weight aluminum foundry to companion with, guarantee they have substantial market experience and are educated regarding all elements of the light weight aluminum casting process: design, manufacturing, product evaluation, and product screening.
(https://www.cybo.com/US-biz/alcast-company_54)The foundry needs to also have a tested performance history of supplying outstanding products that satisfy or surpass client expectations. Quality assurance needs to likewise be at the top of your list when selecting an aluminum shop. By working with a certified factory that complies with the criteria for quality control, you can shield the integrity of your product and ensure it meets your requirements.
The Alcast Company Statements
By picking a firm who supplies solutions that fulfill or exceed your item needs, you can be certain that your project will certainly be finished with miraculous precision and efficiency. Specific light weight aluminum factories focus on certain types of making processes or casting methods. Various components require different manufacturing methods to cast aluminum, such as sand spreading or die casting.
Die casting is the name provided to the process of developing complex steel components via usage of mold and mildews of the part, also known as dies. It creates more components than any various other process, with a high degree of accuracy and repeatability. There are 3 sub-processes that fall under the classification of die casting: gravity die casting (or long-term mold and mildew spreading), low-pressure die spreading and high-pressure die casting.
After the pureness of the alloy is checked, dies are created. To prepare the passes away for casting, it is vital that the dies are clean, so that no deposit from previous productions stay.
The pure metal, also understood as ingot, is included in the heating system and maintained the molten temperature of the metal, which is after that moved to the shot chamber and injected into the die (aluminum casting company). The stress is then maintained as the metal solidifies. When the steel solidifies, the cooling process starts
What Does Alcast Company Do?
The thicker the wall surface of the component, the longer the cooling time as a result of the quantity of indoor metal that likewise needs to cool. After the element is completely cooled, the die cuts in half open and an ejection system pushes the component out. Adhering to the ejection, the die is shut for the next shot cycle.
The flash is the added material that is cast during the procedure. Deburring removes the smaller sized pieces, called burrs, after the cutting process.
The Single Strategy To Use For Alcast Company
Nonetheless, this proved to be an imprecise test, this link due to the fact that the tester could cut right into an item and miss an area with porosity. Today, leading suppliers use x-ray testing to see the entire inside of parts without cutting into them. This permits them to a lot more precisely accept or reject components. To reach the completed item, there are three main alloys made use of as die spreading product to pick from: zinc, aluminum and magnesium.
Zinc is one of the most used alloys for die spreading due to its reduced expense of raw materials (aluminum casting manufacturer). Its deterioration resistance also permits the parts to be long long-term, and it is one of the a lot more castable alloys due to its lower melting point.
Alcast Company Fundamentals Explained
As discussed, this alloy is just one of the most commonly utilized, yet manufactures will, sometimes, choose light weight aluminum over zinc due to light weight aluminum's manufacturing advantages. Light weight aluminum is highly affordable and one of the extra flexible alloys. Light weight aluminum is used for a variety of different items and industries anything from window structures to aerospace materials.
Report this page